Services

Roofing Services in Florida
One of the most important parts of a building or home is the roof system, which can vary significantly depending on the purpose and location of that structure. For example, a roof in a the north-east will experience heavy snow, which requires having a steep slope to shed the extra weight of the snow, whereas a roof in a hurricane zone will require lower slopes so the consistent high-velocity hurricane winds can glide off the roof. A quality roof system installed by an experienced professional is one of the most important decisions to make and will ensure the maximum protection of your property and its contents, saving you thousands throughout the life of your roof.
Roofing in Florida 101: Crash Course
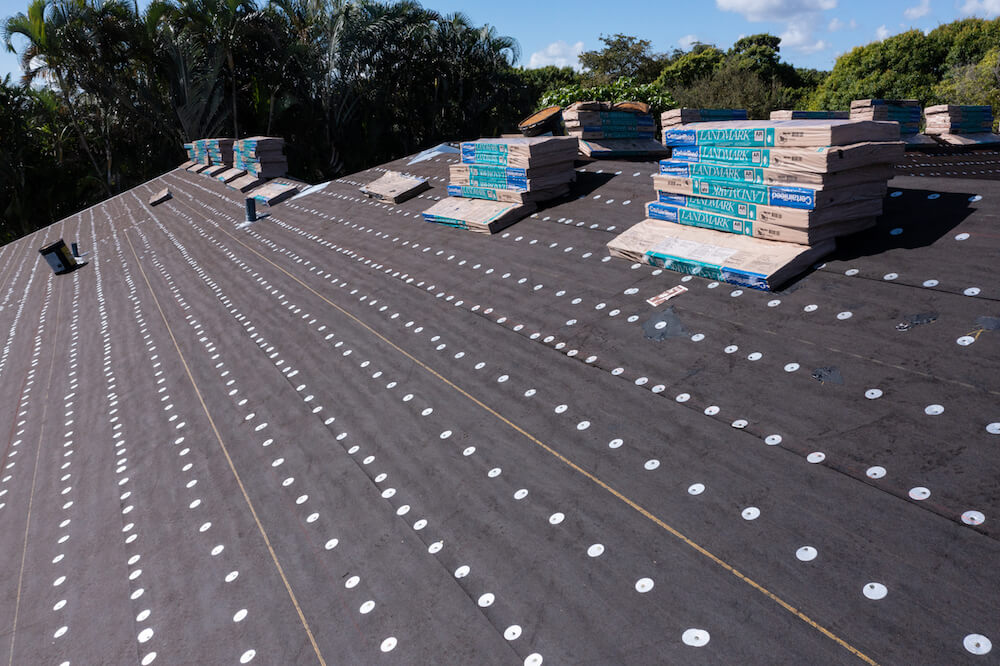
The roofing industry is made up of manufacturers, distributors, and contractors. Manufacturers create the products, submit them for testing, issue warranties, and sell their products in bulk to distributors. Distributors act as the middle man between contractors and manufacturers whenever there is an issue with products or delivery, they may deliver the products directly to the job site, and they usually stock the manufacturers products in bulk in a warehouse. Contractors often refer to the businesses that deal directly with the homeowners and property managers. They are responsible for building the roof system per specifications. They rarely are in contact with manufacturer, but usually have a close relationship with their distributors. Florida Statute 489.113 requires contractors to “establish his or her competency and qualifications” by obtaining a state license in their trade or by having a licensed qualifier on site. This is to protect the consumer from fraudulent contractors. If you are a homeowner or a property manager, it is important for you to know who is involved in the project. If your contractor is organized and professional, you may never need to speak with the manufacturer or the distributor. Read more on Florida Statutes 489 here.
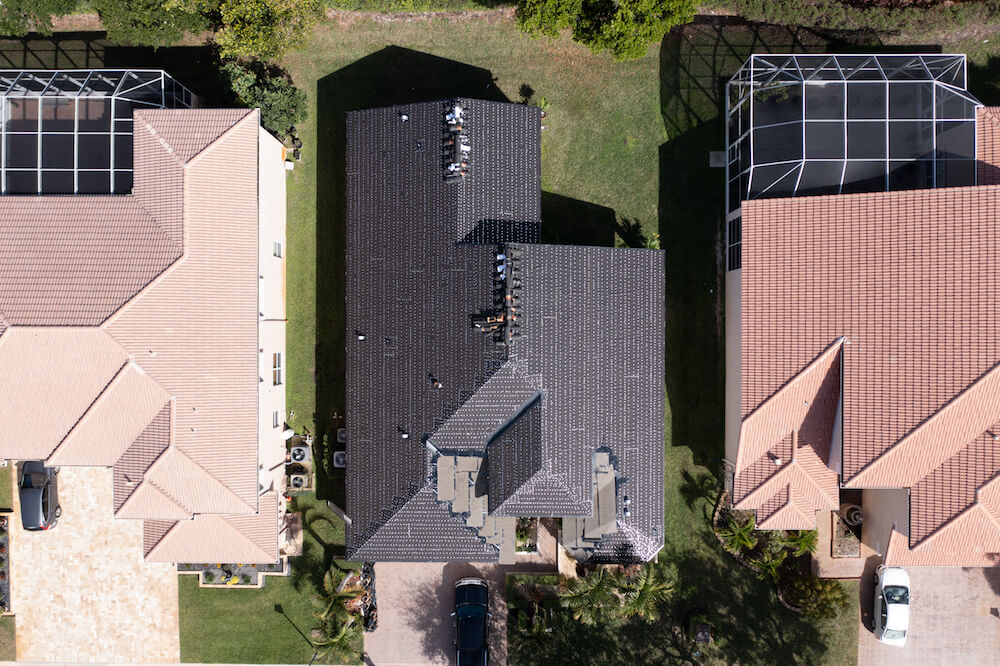
In Florida there are primarily five types of roofing systems – Concrete Tile, Clay Tile, Asphalt Shingle, Built Up Flat Roofs, and Metal. Technically there are many more, but these are the most popular and are categorized by what you can see at the completion of your roof. This little known fact is what makes roofing so complicated because you usually cannot see what is underneath the surface. Each type of roof system can be assembled in a dozen different ways with different product combinations we refer to as roof assemblies. Typically the manufacturer will recommend specific products in the roof assemblies specifications to meet the requirements for their independent manufacturer warranty and to meet building codes. All the products used in a roof system should have a Florida Product approval or Miami-Dade Notice of Acceptance (NOA). These certificates ensure that the products used on your roof have passed rigorous testing by independent testing facilities. Basically, the State of Florida is protecting consumers to ensure that they are spending their money on products that work. Search for Florida Product Approvals HERE. Search for Miami Dade Notice of Acceptance HERE.
Below you will see what a roof deck looks like without a roof system to cover it, and and on the right you will see what the first layer of underlayment looks like for pretty much every roof system in South Florida with slopes greater than 3:12. In this case the first underlayment is a #30 felt nailed to a wood deck. Many non-HVHZ (high-velocity-hurricane-zones) allow the use of self-adhered underlayments applications direct to deck.
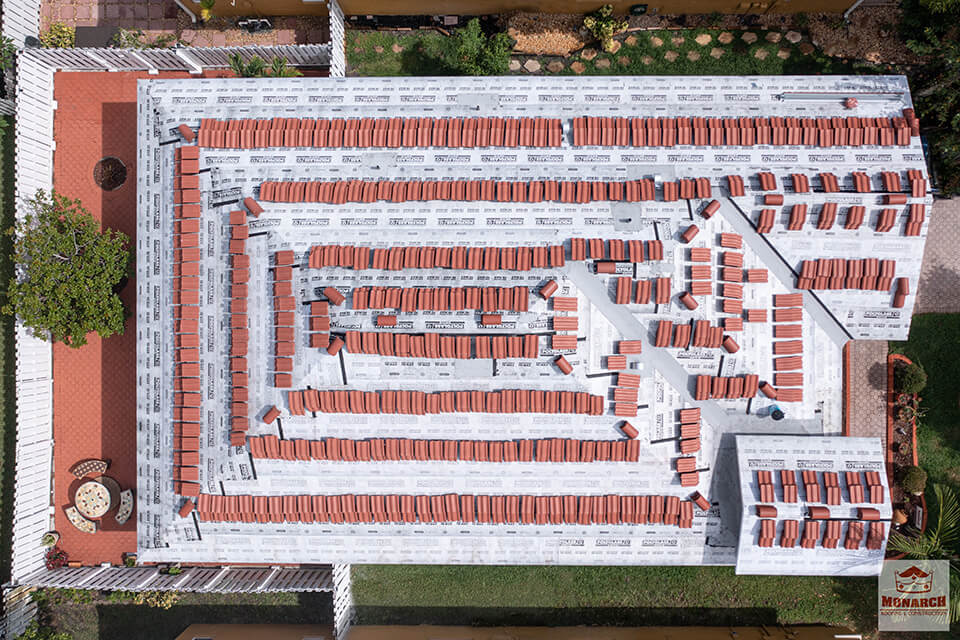